Your needs. Our benchmark.
We take your gas turbine operation to a whole new level
The optimum operation of gas turbines is crucially dependent on external and often uninfluenceable parameters, such as ambient temperatures, humidity, air pressure, but also parameters such as gas quality, gas pressure or gas temperature.
These variables change constantly during operation, sometimes very quickly and unpredictably. The gas turbine must therefore constantly react to external changes.
But can it really do this? The answer is no.
The gas turbine control system cannot react to the above-mentioned constant changes in the external influencing variables, which means that the machine would theoretically have to be constantly readjusted in order to achieve optimum operating conditions.
For this reason, gas turbines must be readjusted from time to time by qualified personnel and experts (Tuning).
But human intelligence can not recognize 6 to 8 simultaneously changing boundary conditions and act accordingly!
Our solution: ”Predictive Operation“
We want to enable operators of fossil-fuelled power plants to optimize the operation of their gas turbines at any time.
Our AI-based software solution combines current technologies (Artificial Intelligence) with the principles of machine learning, as well as years of human experience in the field of combustion and operational optimization of gas turbines.
Our software uses the existing historical data of the machines, learns from it, trains its models and applies this knowledge for precise statements for computer-optimized gas turbine operation – and combines a variety of aspects of operational optimization:
– Combustion stability
– Operational safety
– Emission optimization
– Performance optimization
Fore more and detailed information download the IPSUMA booklet.
Next-level gas turbine monitoring and optimization
The idea of IPSUMA
IPSUMA is a intelligent performance software using maschine-based learning applications. This brand new type of software and first of its kind enables operators of fossil-fuelled power plants to optimize the operation of their gas turbines at any time.
Optimum gas turbine operation depends on many different external factors. Many of these factors cannot be controlled or regulated by the operator. These include ambient temperatures, air humidity, air pressure, but also aspects such as gas quality and gas pressure. On the other hand, there are also controllable factors that influence gas turbine operation. These include, for example, the pilot gas and the calculated exhaust gas temperature (TOTC).
All these external uncontrollable factors change constantly during operation and thus exert a considerable influence on the quality of gas turbine operation. In many cases, this leads to deviations in operating quality, sometimes significant, such as reduced output, combustion instabilities, which in the worst case can lead to operational failure, but also increased pollutant emissions beyond the upper limits permitted by the authorities.
We are therefore dealing with a multi-dimensional influence of various external factors on the quality of optimum gas turbine operation.in the past, gas turbines had to be optimized again and again by specialized personnel in such cases. The planning and implementation of such measures alone ties up resources, time and money on the part of the gas turbine operator.
But is everything good again after a gas turbine operation optimization, even if it has been successful? Is the gas turbine permanently optimized in the long term after a successful optimization? Can a specialized combustion and operating engineer even record all existing external factors at the same time and adapt his optimizations accordingly?
The answer to all three questions is a clear no. Even after a (successful) optimization, the various external factors will continue to influence the apparently optimized operation and the cycle of measures will start all over again.
But is there no solution to this? How can a gas turbine operator ensure that the gas turbines run optimally at all times, even under changing boundary conditions?
The solution is IPSUMA and was developed by Lenja on the basis of almost two decades of relevant experience in the field of gas turbines and fossil energy conversion.
IPSUMA is a locally applicable software that utilizes the latest in artificial intelligence and machine-based learning.
IPSUMA combines and unites the experience and knowledge of combustion technology operating behavior with the possibilities of artificial intelligence.
IPSUMA contains the necessary specific expertise and analyses the influence of all existing external factors of gas turbine operation through the use of artificial intelligence with the aim of providing the operator with an optimized gas turbine at all times.

Next-level gas turbine monitoring and optimization
How does IPSUMA work?
IPSUMA learns continuously during operation. The specially developed AI algorithm analyses complex influencing factors and draws a complete picture of the gas turbine's operating behaviour. This is the only way to optimise important output variables such as emissions, efficiency or electrical output. IPSUMA combines all these requirements.
IPSUMA is analysis and optimization software and is directly available to the operator for full-time use in the power plant.
Our software is based on the permanent use and analysis of the historical operating data of the gas turbine. Over time, this results in an ever-growing pool of data, which leads to ever more comprehensive and complete operating experience and, as a result, paints an ever more accurate picture of the optimized gas turbine.
The operating data is summarized, collected and filtered in an internal database. This ensures that only meaningful and plausible data sets are used for IPSUMA’s learning process.
IPSUMA is constantly learning with the greatest possible effectiveness
With the use of our specially developed and unique AI algorithm, continuous optimization of the gas turbine, which can be carried out independently by the operator, is possible at any time.
Our AI algorithm is able to record and analyze all existing external boundary conditions that have an influence on the machine behavior and draw the correct technical conclusions from them.
It is important to note that all relevant limit values for monitoring the stability of the gas turbine are preset by experts from Lenja Enginnering.
This means that all operating scenarios calculated by IPSUMA are within the safe operating range of the gas turbine. IPSUMA continuously compares the measured combustion-related operating behavior with the actual boundary conditions.
We are convinced that the potential of the machines can be achieved in the best possible way by using historical and current operating data. We have not lost sight of the priorities of the optimization process and have developed IPSUMA accordingly.
The first priority is combustion stability. If this stability is not available, gas turbine operation is generally not possible.
Once the first priority has been met, the second comes into play, namely achieving the lowest possible pollutant emissions (NOx and CO). We should be aware of our responsibility in the area of fossil energy generation to make an important contribution to the preservation of our planet and to take our self-imposed climate targets seriously and act accordingly.
Once the previous two priority levels have been met and the gas turbine shows further potential, priority level 3, performance and efficiency, comes into play.
Here too, IPSUMA can ensure that the efficiency and technical performance of the machine is optimized.
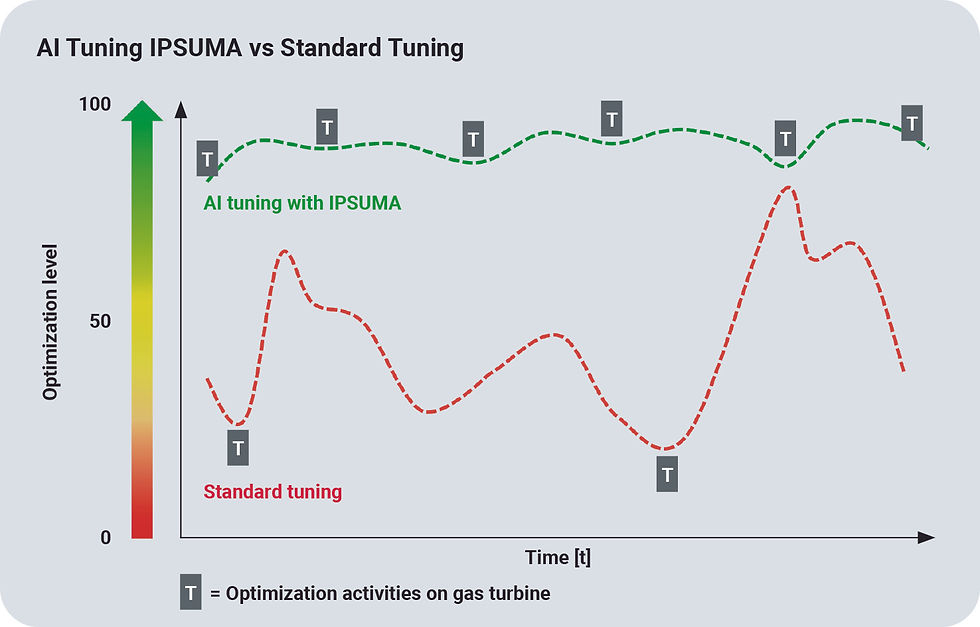
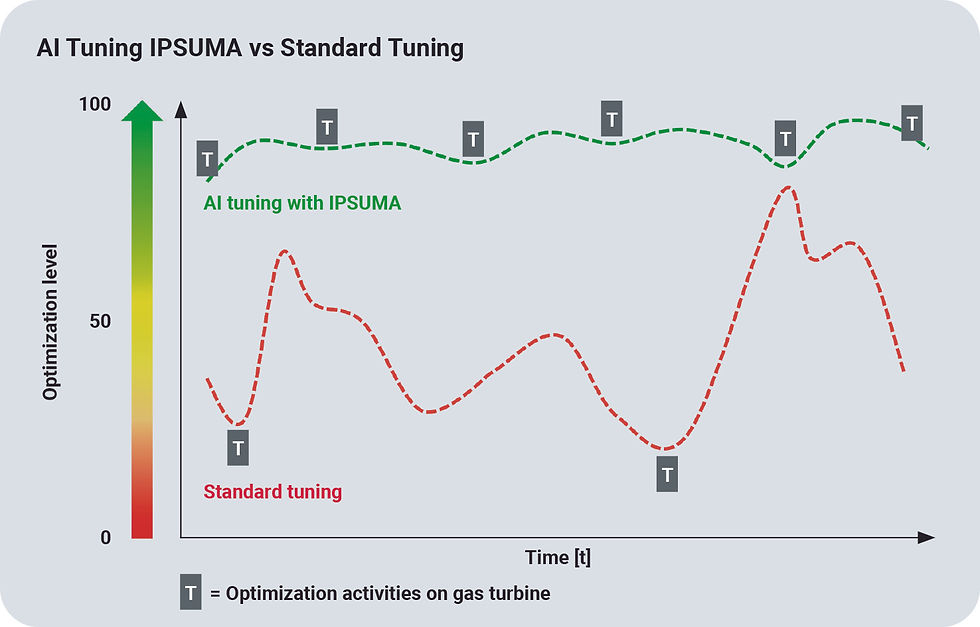
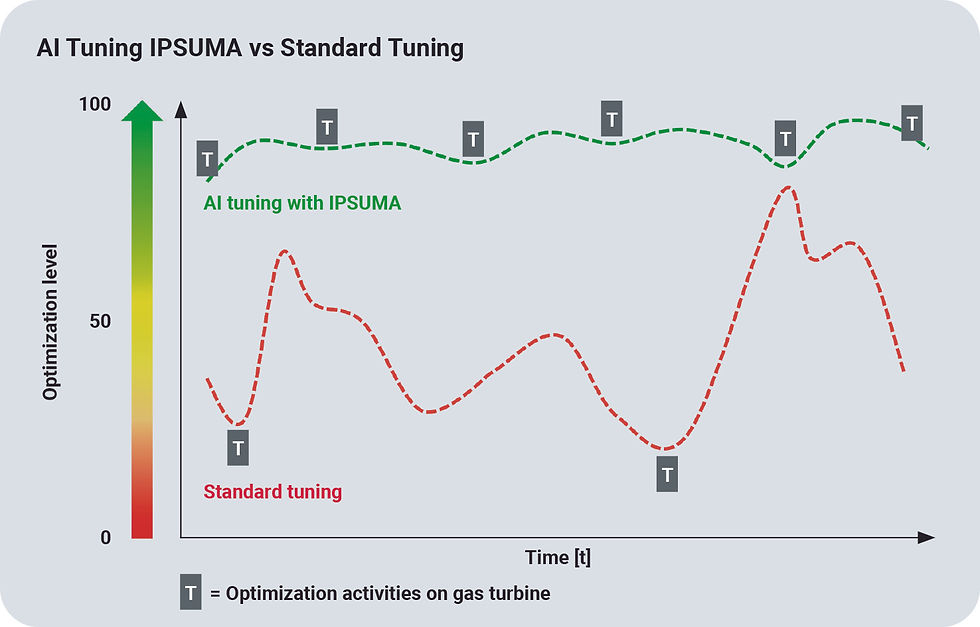
Next-level gas turbine monitoring and optimization
Working with IPSUMA
IPSUMA is a locally installed software and can be used directly on site by the operating personnel. IPSUMA offers a wide range of possible applications. From the optimisation of the current operating status to the planning and assessment of future operating scenarios. All with one goal: optimized, safe and sustainable gas turbine operation at highest technical level.
The use of IPSUMA should be simple, understandable, comprehensible and, above all, targeted and effective for the operator. IPSUMA offers a clear and structured user interface (GUI) to enable the user to familiarize themselves with the product as quickly as possible.
IPSUMA is divided into a user area and an admin area
The user area lists all existing boundary conditions (controllable and uncontrollable), as well as the current operating point of the gas turbine and the currently associated machine reactions (accelerations, emissions, other combustion measurement parameters). In the admin area, the user can define various operating scenarios (setting limit values) that serve his current technical interests.
The user area contains the two main functions of IPSUMA
1. CALCULATE The Calculate function is the main optimization function of IPSUMA. This function analyses the combustion-related operating behaviour of the gas turbine on the basis of all the operating data available in the internal database, compares this with the stored stability criteria and calculates the new, optimized, controllable operating parameters (pilot gas and TOTC) using the special AI algorithm.
The operator can then implement this result in the gas turbine control system. With this function, it is therefore possible for the user to optimize their gas turbine at any time in the event of changing uncontrollable boundary conditions.
These can be fluctuations in gas quality or gas pressure, but also seasonal or daily differences in ambient air and air pressure. This enables the user to replace the non-optimal ACTUAL value (pilot gas and/or calculated flue gas temperature value) with a new, optimized TARGET value.
2. PREDICT The Predict function offers a further attractive approach to the continuous operational optimization of gas turbines. Instead of determining new and optimized operating parameters, this function takes the opposite approach.
This means that the user can specify self-selected controllable settings (pilot gas and/or calculated exhaust gas temperature) as well as uncontrollable framework conditions and IPSUMA mathematically determines the effects of these (fictitious) operating settings on the operating behavior using the special AI algorithm and provides a corresponding probability of occurrence forecast.
This function is particularly suitable for operational planning, e.g. for expected changes in gas quality, gas pressure changes or weather changes. The Predict function is therefore an equally important and useful contribution to maintaining the operational reliability of the gas turbine at the highest possible level.
Use of AI in the operation of gas turbines
How to maximize the security of supply and efficiency in energy supply
Seamless monitoring, continuous analysis of machine statuses and corresponding optimization of the machine 24/7 are necessary for the security of supply – and to increase effiency and reliability. An outage due to service times, malfunctions or damage would cause an enormous impact and would lead to a loss of sales and investments.
Our aim is to ensure optimum operation of gas turbines under every possible working condition – in terms of efficiency and security of supply. With the use of AI-based software.
However, this cannot be achieved with the systems currently available and their control by service personnel. The amount of data and information, the simultaneous comparison of historical and actual data and the possible initiation of appropriate measures during operation are beyond the capacity of human management.
You need to rethink and change your previous ways of doing things. We call it "Preventive Operation"
The result is mindblowing: Monitoring and optimization of your gas turbines on a completely new level – to maximize security of supply and efficiency in energy supply.
We accompany our customers on exactly this path and develop flexible solutions that make it possible to significantly reduce downtimes and optimize reliability and efficiency – for this purpose, we identify suitable measures in the respective processes for the gas turbines used with the help of our AI-based software.
To do this, we identify suitable measures in the respective processes for the gas turbines used with the help of our AI-based software. Sustainably. With greater efficiency. And with lower running costs, as downtime and maintenance times can be minimized.

Sustainable power generation thanks to AI
Sustainable power generation with your gas turbines. Reaching the goal successfully thanks to AI support.
Every company in the energy sector want to increase sustainability in the operation of gas turbines, while at the same time increasing efficiency – without increasing costs.
This cannot be achieved with the systems currently available and their control by service personnel. The amount of data and information, the simultaneous comparison of historical and actual data and the possible initiation of appropriate measures during operation are beyond human management capability.
Our aim is to ensure optimum operation of gas turbines under every possible working condition – in terms of efficiency and reducing emissions. With the use of AI-based software for seamless monitoring, continuous analysis of machine conditions and corresponding optimization 24/7.
We accompany our customers along this path and develop flexible solutions that enable them to successfully achieve ambitious reduction targets.
This is the moment where our solution comes into play: "Preventive Operation"
Monitoring and optimizing your gas turbines to a whole new level for more efficient and sustainable power generation!
To do this, we identify suitable measures in the respective processes for the gas turbines used with the help of our AI-based software. Sustainably. With greater efficiency. And with lower running costs, as downtime and maintenance times can be minimized.

How to secure machine data
Achieve maximum safety when monitoring and optimizing your gas turbines – with our locally installed AI software
When it comes to the remote maintenance of your gas turbines, security plays a key role. It is not only the possibility of unauthorized access from outside and the theft of sensitive data that makes many companies hesitate on this subject. Perhaps you are too!
A disruption to production processes or damage to your gas turbines – the worst case scenario.
We are aware of this problem and offer our customers intelligent solutions for monitoring gas turbine machine conditions, with complete analysis of all available machine data and control and optimization. 24/7. And no external access is possible – securely, thanks to our locally installed software.
This does not necessarily mean that a technician has to be on site at all times. On the contrary: our solution approach means a significant reduction in your service, maintenance and repair costs.
We call it "Preventive Operation“
We rely on locally installed AI-based software that enables you to monitor your machines absolutely securely and reliably, with access to all relevant data 24/7 for maximum availability and the best possible machine condition.

Road to Net Zero – more targeted with AI
Road to net zero emissions in the operation of gas turbines. Reaching your goal faster and more efficiently with our AI-based software.
There is currently no other solution: we must drastically reduce global greenhouse gas emissions over the next 25 years in the interests of climate protection and a sustainable way of life in order to avert a further increase in global warming.
To achieve the necessary system change, strategies must be consistently implemented and technologies must be optimally used and further developed in order to reach the proclaimed net zero target.
Our AI-based software solution helps companies in the energy sector to achieve their net zero target
Reducing emissions is a priority in the fight against climate change. Companies can work towards their own net zero target by reducing emissions as much as possible and neutralizing remaining emissions.
For example, gas turbines that are used to generate energy must be operated optimally under every possible working condition – in terms of efficiency and, above all, in terms of emission values.
This cannot be achieved with the systems currently available and their control by technicians and service personnel. The amount of data and information that needs to be processed simultaneously in order to analyze the current status and draw any necessary conclusions for ongoing operations is beyond human capacity.
The path to Net-Zero will therefore be a revolution in both technology and mindset. This path will require us to rethink and change the way we have always done things.
We call it "Preventive Operation": monitoring and optimizing your gas turbines on a whole new level!
We have set ourselves the goal of developing suitable, flexible solutions for our customers on the path to Net-Zero – such as AI-based software that makes it possible to achieve these ambitious reduction targets. This enables us to identify suitable measures in the respective processes for the gas turbines used and ensure optimum performance and efficiency.

More efficient and proactiv with AI
We protect your investments with AI-supported software
For you, continuous machine availability in regular operation is essential for the stable and reliable production of electricity/energy.
Various measures are required to minimize machine maintenance or downtimes – preventive measures such as an efficient maintenance strategy, regular maintenance work and routine checks.
Certainly nothing new for you, but…
Simply go one step further with us and avoid scenarios that lead to machine downtime. We are not talking about "predictive maintenance" – our solution goes far beyond that.
What exactly is the next step? Rethinking!
We offer you a completely new and revolutionary solution that makes it possible to check and monitor the condition of the machine 24/7 – including all historical data, the actual condition and a resulting assessment of which parameters require optimization.
Our aim is to avoid reactive measures and to make suitable changes to the machine during operation before a possible scenario arises – based on historical and current data.
Information that would otherwise have to be checked and assessed by service personnel/technicians. Due to the large amount of information, a reliable analysis and initiation of procedures, e.g. in the event of an (imminent) malfunction, cannot be carried out optimally. The technician would have to be able to analyze and assess all the data available to him at the same time in order to derive suitable measures.
Rethink monitoring and optimization of your gas turbines. Take the next step with "Preventive Operation“
We go one step further: our AI-supported software analyzes all available information – such as constantly changing ambient temperatures, changing humidity, fluctuating gas quality, changing air pressure) and constantly compares it with historical and current machine data.

Breaking new ground
Opportunities and benefits: AI-based software for monitoring and optimizing your gas turbines
An AI-based software solution offers you the opportunity to improve the performance, efficiency and reliability of your gas turbines. This leads to cost savings, increased productivity and lower emissions.
Through real-time monitoring and continuous diagnostics, the AI software can continuously monitor the operation of the gas turbine and indicate when deviations or problems occur. This allows technicians to react faster, more purposefully and more efficiently, solving potential problems before they actually occur. These preventative measures reduce unplanned downtime and maximize uptime.
AI algorithms can also optimize the operating parameters of your gas turbine to maximize energy yield and minimize fuel consumption. This leads to improved energy efficiency and lower operating costs.
In terms of intelligent load management, AI software can also help you optimize the operation of your gas turbine in real time to respond to fluctuations in demand and maximize efficiency. This allows you to respond optimally to changing electricity demand and adjust the operating parameters accordingly.
Through continuous monitoring and optimization, an AI-supported system can also help to reduce pollutant emissions and improve the environmental compatibility of gas turbines. So that you can easily comply with national and international specifications and standards regarding emission limits.
Rethink your way of gas turbine monitoring and optimization. Use "Preventive Operation“
Our AI-supported software analyses all available information – such as constantly changing ambient temperatures, changing humidity, fluctuating gas quality, changing air pressure) and permanently compares it with historical and current machine data.
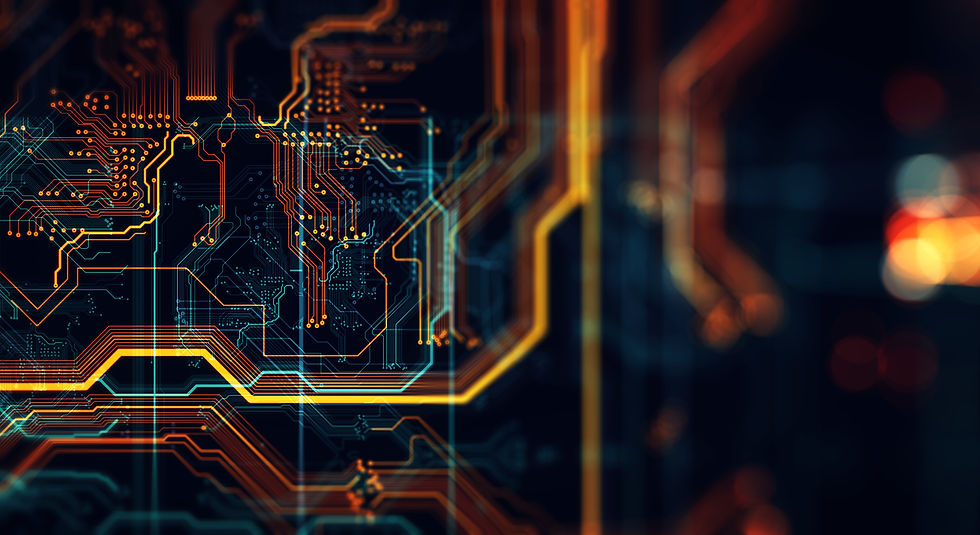
Secure AI-supported software solution
Stay local for the maximum security of your power plant
Software solutions for monitoring and optimizing your gas turbines that constantly communicate with an external server are susceptible to external attacks, such as man-in-the-middle attacks or DNS spoofing, or increase the risk of attacks on cloud infrastructures and enable unwanted external access to the sensitive machine data of your gas turbine.
Locally installed software, on the other hand, offers several security advantages as it does not need an internet connection to operate:
> The locally installed software only saves and processes data on your devices. This means that you always retain full control over the data and can also decide who can access it.
> Without an internet connection and communication with external servers, the risk of data leaks or attacks that could occur via the network is minimized.
> As the locally installed software does not constantly communicate with an external server, it is also less susceptible to unwanted access from outside.
Our AI-supported software is installed locally and can be used locally. It functions completely autonomously. The (optional) connection to the Internet is used exclusively for the purpose of remote support, maintenance measures, error analyses or upgrades and updates.
No operating data needs to be sent or received via the Internet for our software to function. The data processing only takes place on your locally available devices.
We prioritize the security and full availability of your machines and the protection of your investments.
Therefore we want to achieve the highest possible level of operational reliability. We use all our knowledge and expertise to achieve this goal. For you. 24/7.

Use of AI in gas turbine operation: Support, flexibility and reliability
AI support for gas turbine monitoring: trouble-free operation and cost reduction
AI-based software can actively support your employees in monitoring your gas turbines – and help to increase safety to ensure trouble-free operation.
It helps your service personnel and technicians to monitor the operating status of the gas turbine during operation and to analyze all available data seamlessly.
This enables suitable measures to be taken and individual parameters to be optimized with pinpoint accuracy. For the highest possible availability, the best possible machine condition with simultaneous reduction of emissions and lower machine operating costs. And reduces your company costs in the end.
Rethink your way of gas turbine monitoring and optimization. Use ”Preventive Operation“
We therefore go one step further: Our software is always at the side of your service personnel and technicians 24/7 and analyzes all available information – such as constantly changing ambient temperatures, changing humidity, fluctuating gas quality, changing air pressure) and permanently compares it with the historical and current machine data and, if necessary, supports the setting of specific parameters in order to achieve, maintain and further improve the optimum machine condition. For maximum availability, maximum reliability and an operating condition that allows the machine to work more efficiently and with lowest possible emissions.
”Preventive Operation“: In time optimization, planning and forecasting. All in one.
Our AI-based software solution is your digital partner partner on the way to reliable, clean, safe and optimized generation of electrical energy.
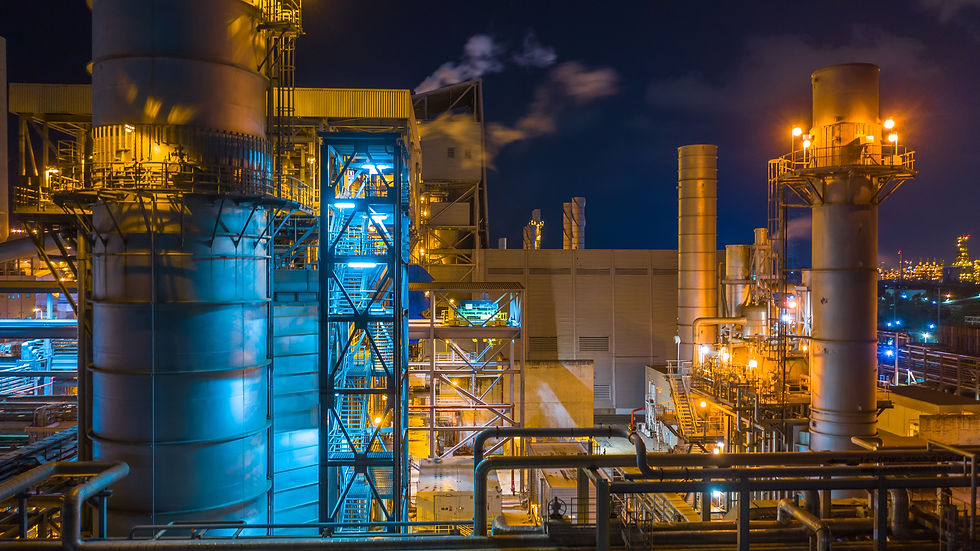